Ultimate Guide: Avoid Faulty Welds On Navy Warships

Introduction to Faulty Welds on Navy Warships

Faulty welds on Navy warships are a critical issue that demands attention and proper understanding. The integrity of welds is paramount for the structural stability and safety of these vessels, which are often subjected to extreme conditions and high-stress environments. This comprehensive guide aims to shed light on the significance of weld quality, the common causes of faulty welds, and the measures taken to ensure their avoidance, thereby maintaining the operational readiness and longevity of Navy warships.
Understanding the Importance of Weld Quality

Welds serve as the backbone of a warship’s structure, connecting various components and ensuring their seamless integration. The quality of these welds directly impacts the vessel’s performance, durability, and ability to withstand the rigors of naval operations. Poor weld quality can lead to a range of issues, including structural weaknesses, leaks, and even catastrophic failures, posing serious risks to the safety of the crew and the effectiveness of the warship.
Key Considerations for Weld Quality:
- Strength and Durability: High-quality welds provide the necessary strength to withstand the stresses and loads experienced during naval operations.
- Corrosion Resistance: Welds must be resistant to corrosion, especially in saltwater environments, to prevent deterioration and ensure the longevity of the warship.
- Fatigue Resistance: Navy warships are subjected to repetitive stresses, and welds should be designed to resist fatigue and maintain structural integrity over time.
- Weld Defects: Common defects like cracks, porosity, and inadequate penetration can compromise the integrity of welds and must be strictly avoided.
Common Causes of Faulty Welds

Understanding the root causes of faulty welds is crucial for implementing effective preventive measures. Here are some of the primary factors that contribute to weld defects on Navy warships:
Human Error:
- Inadequate Training: Welders who lack proper training and experience may produce substandard welds, leading to defects.
- Fatigue and Distraction: Long work hours and fatigue can impact weld quality, as welders may become less attentive and make mistakes.
- Ineffective Supervision: Inadequate supervision during the welding process can result in oversight of defects, allowing faulty welds to go unnoticed.
Equipment and Material Issues:
- Welding Equipment: Faulty or poorly maintained welding equipment can lead to inconsistent welds and defects.
- Base Metal Quality: Poor-quality base metals can affect the overall weld quality, especially if they contain impurities or are susceptible to cracking.
- Consumables: Substandard welding consumables, such as electrodes or filler metals, can result in weld defects and reduce the overall strength of the weld.
Environmental Factors:
- Extreme Temperatures: Welding in extremely hot or cold conditions can affect the weld quality, as the base metal may not respond optimally to the welding process.
- Humidity and Moisture: High humidity levels can impact the weld’s ability to fuse properly, leading to defects like porosity.
- Wind and Weather Conditions: Strong winds or adverse weather conditions can disrupt the welding process, causing inconsistencies in the weld.
Preventive Measures and Best Practices

To ensure the avoidance of faulty welds on Navy warships, a comprehensive approach is necessary, encompassing various aspects of the welding process. Here are some key preventive measures and best practices:
Training and Certification:
- Comprehensive Training Programs: Implementing rigorous training programs for welders ensures they are well-equipped with the skills and knowledge to produce high-quality welds.
- Certification and Qualifications: Requiring welders to obtain certifications and qualifications demonstrates their competence and adherence to industry standards.
- Ongoing Professional Development: Encouraging welders to participate in ongoing training and professional development keeps their skills sharp and up-to-date.
Quality Control and Inspection:
- Stringent Quality Control Measures: Implementing strict quality control protocols ensures that welds meet the required standards and specifications.
- Non-Destructive Testing (NDT): Utilizing NDT techniques, such as ultrasonic testing or radiographic testing, allows for the detection of weld defects without damaging the structure.
- Destructive Testing: In some cases, destructive testing may be necessary to assess the mechanical properties and integrity of welds.
Equipment and Material Management:
- Regular Equipment Maintenance: Establishing a regular maintenance schedule for welding equipment ensures optimal performance and reduces the risk of defects.
- Quality Control of Base Metals: Implementing strict quality control measures for base metals ensures they meet the required specifications and are free from impurities.
- Consumable Selection: Choosing high-quality welding consumables that are suitable for the specific application and environment is crucial for weld integrity.
Environmental Considerations:
- Climate-Controlled Welding Areas: Providing climate-controlled welding areas helps mitigate the impact of extreme temperatures and humidity on weld quality.
- Weather Monitoring: Monitoring weather conditions and adjusting the welding process accordingly can prevent defects caused by adverse weather.
- Environmental Management: Implementing effective environmental management practices, such as proper ventilation and air filtration, reduces the risk of weld defects.
Advanced Welding Techniques and Technologies

In recent years, advancements in welding techniques and technologies have played a significant role in improving weld quality and reducing the occurrence of defects. Here are some notable advancements:
Robotic Welding:
- Precision and Consistency: Robotic welding systems offer precise and consistent welds, reducing the risk of human error and improving overall weld quality.
- Repeatability: Robots can perform complex welds with high repeatability, ensuring consistent results across multiple warships.
Laser Welding:
- High-Precision Welding: Laser welding provides exceptional precision and control, making it ideal for critical applications and fine welds.
- Reduced Heat Input: Laser welding generates less heat compared to traditional welding methods, minimizing the risk of thermal distortions and weld defects.
Friction Stir Welding (FSW):
- Solid-State Welding: FSW is a solid-state welding process that produces high-quality welds without the use of a melting filler material.
- Excellent Joint Strength: FSW is known for its ability to create strong, defect-free welds, making it suitable for critical structural components.
Case Studies: Successful Welding Projects

Examining successful welding projects on Navy warships provides valuable insights into best practices and the impact of high-quality welds. Here are a few notable case studies:
USS Gerald R. Ford (CVN-78):
- Advanced Welding Techniques: The construction of the USS Gerald R. Ford utilized advanced welding techniques, including robotic welding and laser welding, to ensure exceptional weld quality.
- Comprehensive Training: The welding team underwent extensive training and certification programs, ensuring a highly skilled workforce.
- Quality Control: Rigorous quality control measures were implemented, including NDT techniques, to detect and prevent weld defects.
USS Zumwalt (DDG-1000):
- Innovative Design: The USS Zumwalt featured an innovative hull design, which required precise and high-quality welds to ensure structural integrity.
- Robotic Welding: Robotic welding systems were employed to achieve the required precision and consistency in welds, especially in complex areas.
- Post-Weld Heat Treatment (PWHT): PWHT was utilized to relieve residual stresses and improve the overall strength and durability of welds.
Conclusion: Ensuring Structural Integrity and Safety
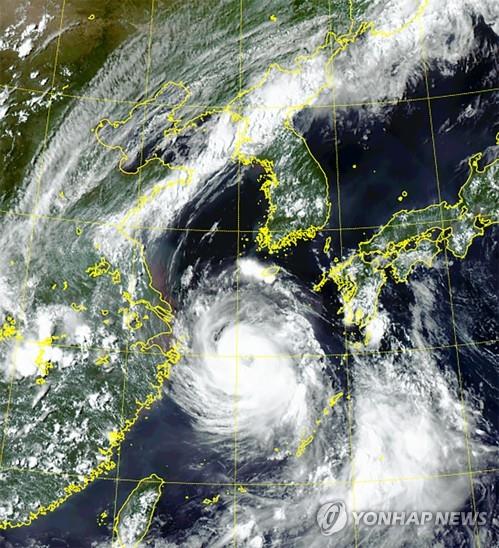
The avoidance of faulty welds on Navy warships is a critical aspect of maintaining the structural integrity and safety of these vessels. By understanding the importance of weld quality, implementing rigorous preventive measures, and embracing advanced welding techniques and technologies, the Navy can ensure the operational readiness and longevity of its warships.
Through comprehensive training programs, stringent quality control measures, and the adoption of innovative welding techniques, the Navy can minimize the occurrence of weld defects and enhance the overall reliability of its fleet. Ultimately, these efforts contribute to the mission-readiness and effectiveness of Navy warships, ensuring they can withstand the challenges of naval operations and protect the interests of the nation.
FAQ

What are the potential consequences of faulty welds on Navy warships?
+Faulty welds can lead to structural weaknesses, leaks, and even catastrophic failures, posing serious risks to the safety of the crew and the effectiveness of the warship. It can compromise the vessel’s integrity and its ability to withstand extreme conditions, potentially resulting in mission failures or even loss of life.
How can robotic welding improve weld quality on Navy warships?
+Robotic welding offers precise and consistent welds, reducing the risk of human error. It ensures repeatability and can perform complex welds with high accuracy, making it an effective solution for critical applications and maintaining weld quality.
What role does quality control play in preventing faulty welds?
+Quality control is crucial for detecting and preventing weld defects. By implementing stringent quality control measures, such as NDT techniques and destructive testing, the Navy can ensure that welds meet the required standards and specifications, reducing the risk of failures.
How can environmental factors impact weld quality on Navy warships?
+Extreme temperatures, humidity, and adverse weather conditions can affect weld quality. For example, high humidity can lead to porosity, while strong winds can disrupt the welding process. Managing environmental factors through climate-controlled welding areas and weather monitoring helps mitigate these risks.
What are some common weld defects found on Navy warships?
+Common weld defects include cracks, porosity, inadequate penetration, and undercut. These defects can compromise the strength and integrity of welds, leading to potential failures. Proper training, quality control, and the use of advanced welding techniques can help prevent these defects.